Coatings
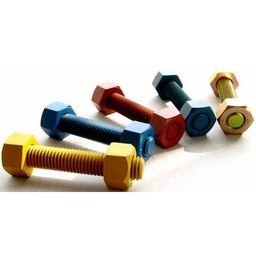
Surface preparation
Xylan coatings (or any thin-film coating) cannot by themselves provide complete corrosion protection. For maximum performance, primers or pretreatments are required.
Types of corrosion-mitigating coatings
These fall into three common categories: barrier, inhibitive and sacrificial.
- A barriercoating stands between the metal fastener and the environment. This is usually an organic coating with fillers that help stop moisture or vapor from permeating the film to the metal and becoming an electrolyte.
- An inhibitive coating is usually an organic coating with corrosion inhibitors, such as zinc phosphates, and chromates. In addition to acting as barriers, they help prevent corrosion by using pigments that provide an inhibitive effect, reacting with the absorbed moisture in the coating, then reacting with the steel to passivate it and decrease its corrosive characteristics.
- A sacrificial coating is usually a metal or inorganic coating containing metal particles (oFen zinc). If the coating is damaged, they act as a sacrificial anode and corrode to protect the steel substrate, sacrificing themselves by galvanic action. These can also be electroplated like zinc or cadmium.
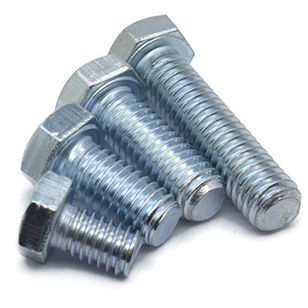
Zinc Electroplating
Zinc electroplating line provides quick turnaround and cost-effectiveness for your plated bolt requirements.
Our zinc plating process, with clear trivalent conversion, offers:
- Hexavalent Chrome Free processing eliminates the toxic chemicals found in yellow chromate.
- Excellent Corrosion Resistance—Exceeding that of yellow chromate, and achieving 200-400 hours to white corrosion in ASTM B-117 Salt Spray.
- Increased Temperature Tolerance to 300-400°F for many hours with no effect on corrosion resistance or color.
- Cost-Effective - This new clear chromate costs no more than yellow chromate.
Electroless Nickel Coating (ENC)
What is Electroless Nickel Coating (ENC)?
Electroless Nickel Coating (ENC) is a technique for applying an even layer of nickel onto a metal surface without relying on an electrical current. This coating serves to enhance the durability of the underlying metal by providing a protective barrier against corrosion, erosion, and abrasion.
BenefitsA cost-effective solution that prevents corrosive chemicals or fluids from penetrating micro-cracks, thereby extending the life of the base metal.
Typical ApplicationsValves, fittings, couplings, collars, piping spools, tanks, vessel/process equipment, packer components, slide plates, downhole equipment, pumps & compressors, rods, casings, and tubulars.
Key FeaturesCompletely amorphous, zero porosity, excellent adhesion (450 MPa), microhardness (550-600 HV), outstanding corrosion resistance, and exceptional uniformity.
Xylan®Overview
Xylan has long been the benchmark of our line of industrial coatings. Registered in most countries around the world, Xylan is used to identify our low-friction, wear-resistant composites of fluoropolymers and reinforcing binder resins.
They are first and foremost dry-film lubricants; however, they have many desirable secondary properties. These lubricants are combined in a matrix with the newest high-temperature organic polymers resulting in “plastic alloys” formulated to provide unique and desirable properties. They can “work” under heavy loads, at high temperatures, in chemical and corrosive environments, and combinations thereof. In the industrial world, they are known as “extreme performance coatings.”
Ten reasons why you should use Xylan coatings:
- Low friction: CoF as low as 0.02.
- Wear resistance: even under extreme pressures.
- Corrosion and chemical resistance in most environments.
- Weather resistance.
- Wide temperature operating range.
Xylan 1070
Xylan 1070 general purpose coatings were the first Xylan fastener coatings, introduced in the mid-1970s and still going strong. They provide outstanding lubrication for predictable makeup and break-out torque, and they have outstanding chemical resistance.
Temperature Range: -425°F (-255°C) to 550°F (290°C) continuously.
Xylan 1070 has added corrosion inhibitors.
Xylan 1424
Xylan 1424 is the environmentally friendlier version of the 1000 series coatings. Xylan 1424 series coating can be made in any color, including white. They also have better chemical resistance to bases than the 1000 series.
Xylan 1424 series reaches complete cure at 400°F (205°C), ideal for most coating operations.
Xylan 1424 series coatings work best for onetime installations, where the fastener will be coated, installed, and let alone.
Temperature Range: -40°F (-40°C) to 350°F (175°C).
6. Flexible curing schedule: ambient to 750°F (400°C).
7. Wide color range: color-code your product.
8. Pliability.
9. Machinability.
10. Excellent adhesion